A fundamental goal of NEWMATT consists of the design, development and production of “green” filaments and fibers to be used as feedstock of Fused Deposition Modeling (FDM), and/or as reinforcing elements of next-generation composite materials.
Our main focus is on polymer matrix filaments enriched with natural, and recycled reinforcing particles, including recycled nylon, and rare earth metals. Such materials are combined in suitable proportions to achieve reinforcing fibers of composite materials and 3D printing filaments/powders. In most applications, waste materials are blended with suitable polymeric material and extruded in the form of FDM feedstock filament. When using magnetic particles as reinforcements, NEWMATT filaments are able to change their properties under the influence of external stimuli such as current, magnetic field, etc., and are well suited for 4D printing applications (that is, the additive manufacturing of customized prototypes/functional parts that can change shape/properties with time).
The interest of NEWMATT toward such fibers and filaments is multifold: i) achievement high physical and mechanical properties in sustainable composites; ii) reduction of manufacturing costs; iii) mitigation of the environmental problems created by the disposal of plastic and electronic waste in landfills, or their floating in the oceans.
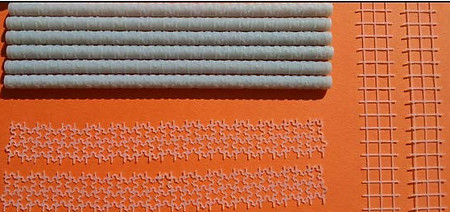
Green fibers and filaments


Fibers and filaments obtained from recycled materials: (top) recycled PET (R-PET) fibers obtained through the recycling of post-consumer plastic bottles; (center) recycled nylon (R-NYLON) fibers obtained from waste fishing nets; (bottom) R-NYLON filaments for 3D printing.
Recent studies have shown that composite materials showing multiscale fibers coated with carbon nanotubes feature enhanced interlaminar shear strength, a key property of composite materials that can be weak in the presence of smooth matrix-fiber interfaces. It is also known that most natural shapes exhibit hierarchical organization of matter and fractal geometries, which provide increased surface area for the same volume of material. NEWMATT employs 3D printed lattices with hierarchical structure to form fabrics, fibers and coatings of groundbreaking reinforcements for novel composite materials. Short and long fibers with structural hierarchy originating from their geometric design are directly manufactured from CAD data, employing additive manufacturing techniques based on polymeric and metallic materials. An initial source of hierarchical architecture arises from using fibers covered by a lattice on a smaller scale. A second strategy employs lattices with fractal geometry to form multiscale fabrics, and coatings, cross-sections or junctions/embossments of multiscale fibers. A third approach makes use of nanoscale coating and/or plasma irradiation techniques.
​
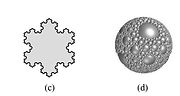
Lattices with fractal geometry used to form reinforcements of composite materials: (a) fiber coating; (b) fabric; (c) fiber cross-section; (d) junction element/fiber embossment (Apollonian sphere packing); (e) 3D printed parts.
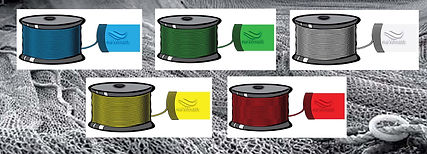
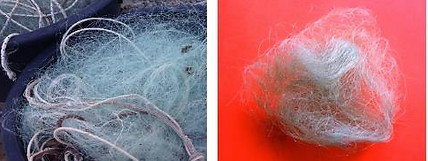